
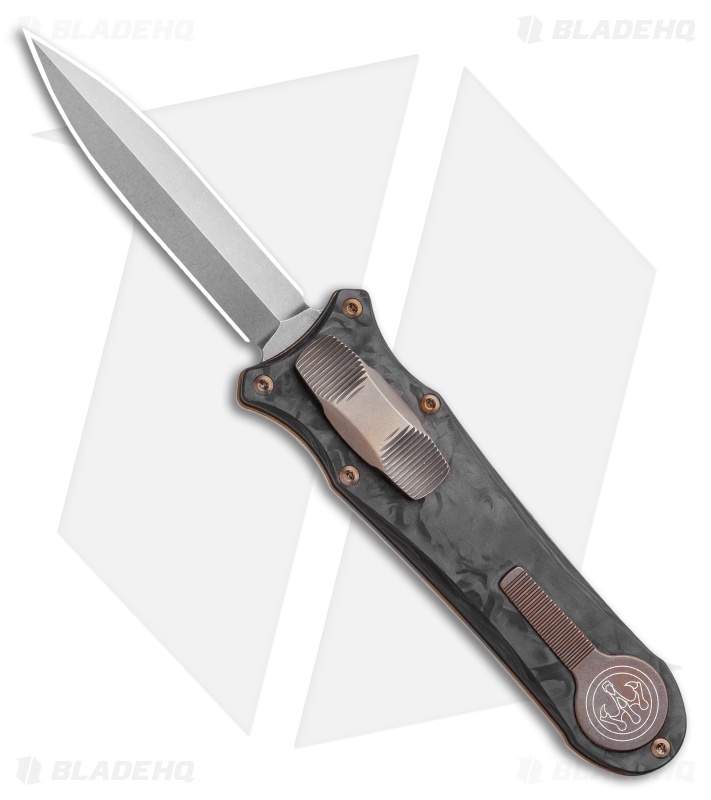
The first Deadlock Model C prototypes will be offered for sale at Blade Show this weekend. Stay tuned for teaser shots of the knives we will be bringing with us. We made a very conscious decision to go forward as a high-end manufacturer, and we’ve been very happy with our decision.” And as far as production collaborations or the like go, Hawk says there won’t be any. The Deadlock Model C will be Hawk Knives’s main focus going forward. Once the basic workflow is established, the Hawks will work on variations with different inlays and blade steel – things that never happened with the Model B, due to the time intensive construction process. “It’s still early to know how that will actually work in reality, but I suspect we will be able to put out a lot of these,” Hawk tells us. These changes should let the Hawks do something with the Deadlock that they’ve wanted since the beginning: produce it on a larger scale.
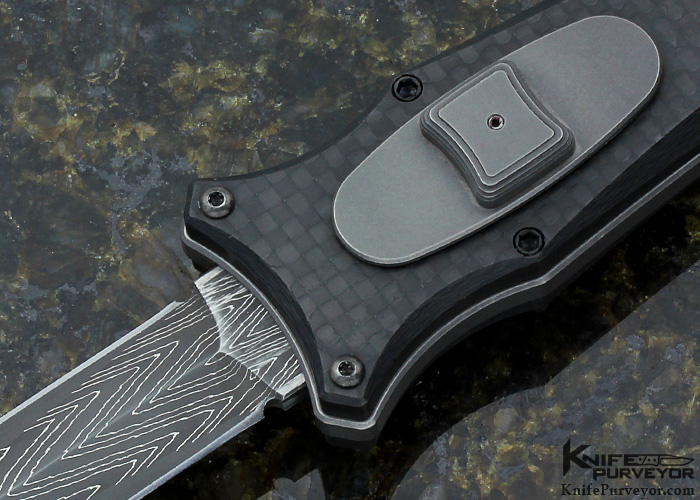
I literally look at Model C and think, Wow I designed that!” “I’m sure I’m a little biased but I really like the way the aesthetics of the Model C turned out. So the major components can be screwed down and held solid.” Hawk also notes that the Model C is the best the Deadlock has ever looked. It also means that we have one main component that all other parts fasten to. “On the Model C we are using a two-part construction which makes for a more rigid handle, and easier to machine parts. “In the Model B we used a three-piece construction that included two overlays and a frame that were sandwiched together,” says Hawk.
#Deadlock knife manual#
While the manual M.U.D.D knife is a mile stone unto itself, having a completely sealed automatic M.U.D. The new frame also reduces the overall part count. This design was always intended to be an automatic, its just taken a few years to come to fruition. And that if we could just go to a smooth blade channel things would improve, and they definitely did.” “I knew that a lot of our issues we were having in assembly were the result of a rough blade channel. “It’s amazing how much better the knife works from the standpoint of repeatable lockup,” Hawk tells us. This made the rails’ surfaces both durable, and very smooth. This was a constant issue in assembly.”Īn aluminum frame meant that the Hawks were able to implement a type III hard anodization. “This was a very time-consuming process that made the surface hard, but not very smooth. To counteract the galling, Model A and B Deadlocks had their interior blade channel rails carbidized to prevent wear over time. Which is why a lot of knife makers put steel inserts into their frame locks, or carbidize the lock face,” Hawk explains. Previous Deadlock models had frames made from titanium, but the Model C is made from aluminum instead. The really big news is the cycle tests! By changing a few parts around, and applying various coatings, we have achieved cycles of 100,000 on all parts! Spring breakage is the number one failure of other OTFs on the market.The new Deadlock Model C is made from aluminum, not titanium.

The older versions were smoother and easier to operate than all other OTFs on the market, but this new version is by far the smoothest out-the-front available to date.īy making the internal mechanism with even less parts, and with screws with all the same size torx, taking the knife apart is easier than ever.
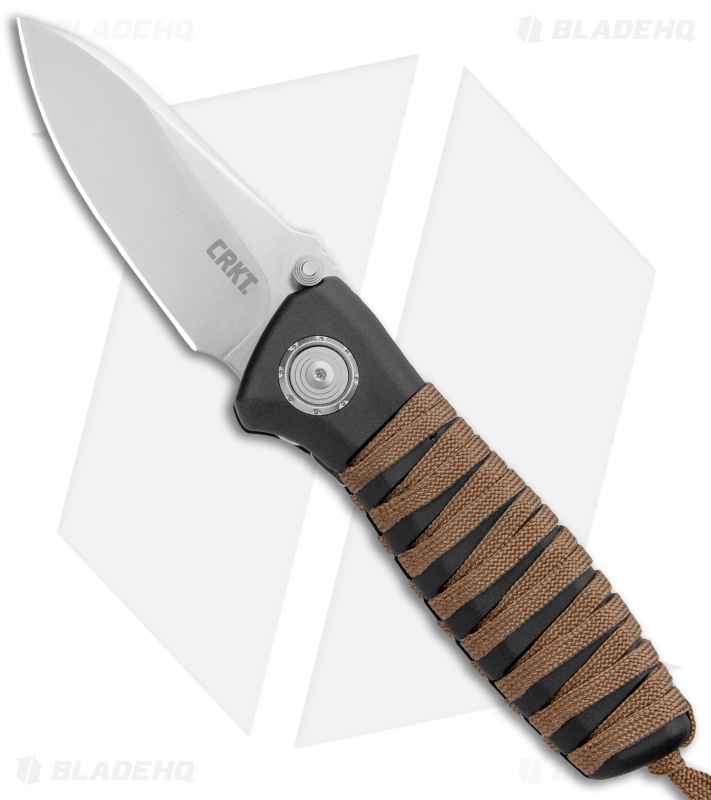
This version of the Deadlock is so smooth. In Batch 4 and 5, we focused on number of overall cycles, smoothness, ease of user disassembly, and of course- ease of manufacturing. Batch 2 is fairly easy to take apart, while Batch 1 and the prototypes are best sent back to me when the time comes. Batch 3 was again ease of manufacture, with an added focus on the ability for the user to take the knife apart for cleaning. The goal of Batch 1 and Batch 2 was ease of manufacture, which came in the form of simplification. The first prototypes had a singular goal of locking up solid. Every batch of Deadlocks has started with a goal.
